

Anthony’s knowledge and connections with suppliers makes him a key player to our team’s ability to deliver products to market. Kevin’s knowledge of embedded systems programming has played an important part in successfully bringing PLX products to market.Īnthony Chew – Responsible for manufacturing, testing, and quality. Kevin Kwong – Responsible for firmware and electronic components. He has successfully taken over 35+ products to market for PLX Devices Inc. Paul Lowchareonkul – Paul is the project leader and chief designer of the Luxor 2.
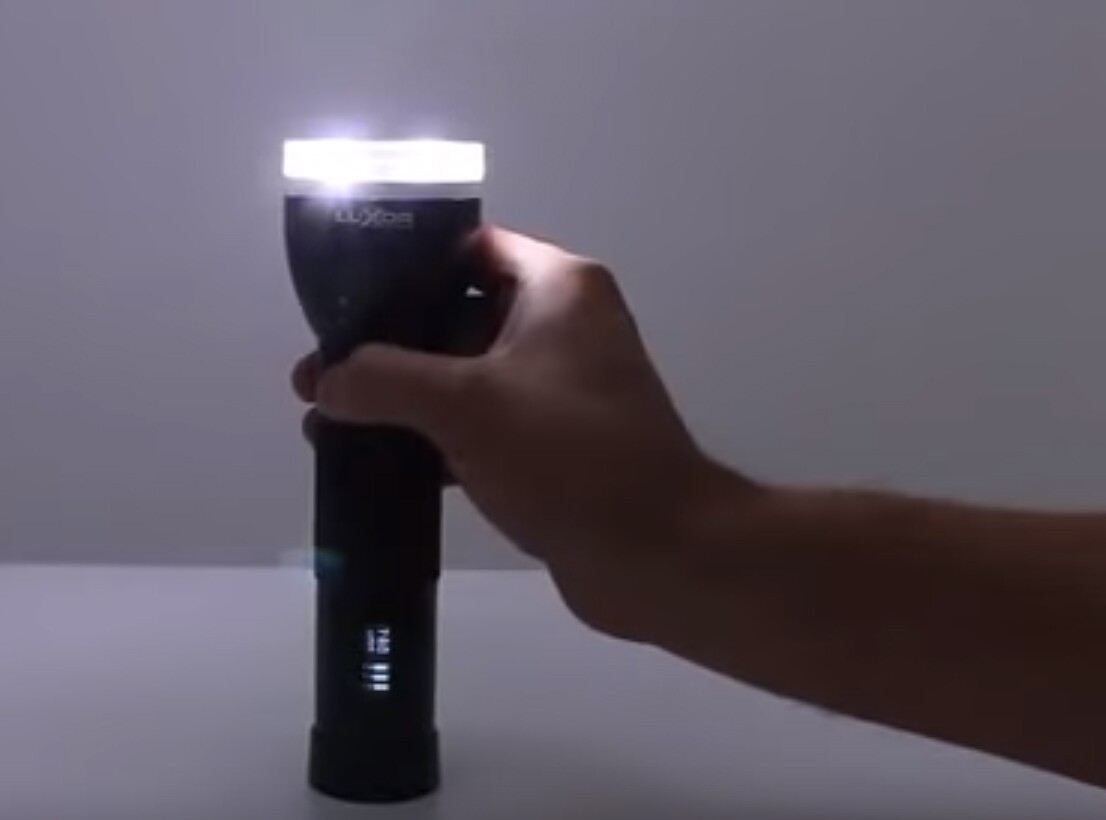
Luxor’s spacers and holders will be made from high grade, impact resistant plastic. Plastic – Manufacturing the internal plastic components of Luxor requires a process called injection molding. Luxor’s complex electronics requires that the PCB be manufactured with the tightest of tolerances to ensure reliable electrical connections between the numerous components to be placed on it. A final protective coating is then applied to create the final finish.Įlectronics Manufacturing and Assembly – Manufacturing the electronics requires a printed circuit board (PCB) made of fiberglass base board with copper interconnects.
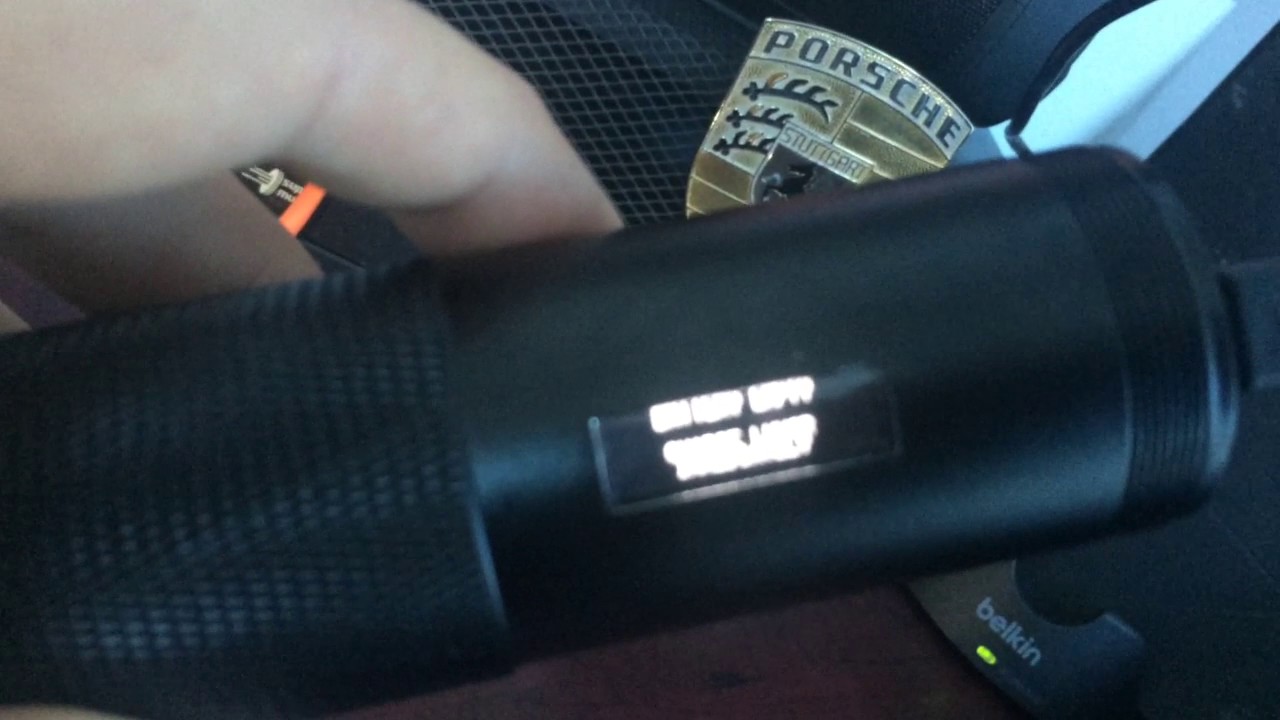
Once the aluminum is in its final shape and form, it will be sanded and polished to create a smooth and shiny luster. We’re confident that our manufacturing resources, connections, and infrastructure will be able to deliver Luxor into your hands according to our delivery schedules.Īluminum – Manufacturing Luxor’s head and body requires machining. We have successfully fulfilled 4 Kickstarter projects with our tried and true methods.
